Integrated report 2019
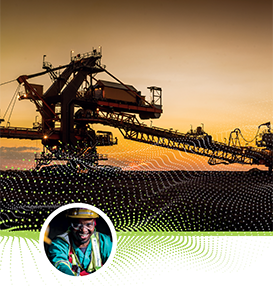
Grootegeluk mine is on the southern margin of the Waterberg coalfield, south of the Daarby fault on the shallow opencastable portion of the coalfield. The mine is 25km west of the town of Lephalale in the Lephalale magisterial district of Limpopo, South Africa. Grootegeluk can be reached from Lephalale via the hard-topped Nelson Mandela Drive, which is linked to the R510 road connecting Lephalale to the town of Vaalwater to the south and the Stockpoort border post between South Africa and Botswana to the north.
Grootegeluk comprises one open-pit mine which includes two overburden benches, nine RoM benches and three interburden benches. RoM is transported to the Grootegeluk beneficiation complex via hauling trucks and conveyor belts. The beneficiation complex consists of eight plants producing several different coal products to client specifications. Beneficiation plant discard is backfilled into the mined-out portion of the open pit while slimes are pumped to a specially designed cyclic pond system from where it is later reclaimed and blended in low quantities with the power-station coal produced.
The mine is linked to the suburb of Onverwacht, the town of Lephalale and neighbouring towns, as well as nearby border posts with Botswana via the R510 road.
Power supply to the mine is obtained directly from the power station, via two 133kV lines that supply the mine's 40MVA transformers, which in turn distribute 33MV through two measuring points to the plant and mining operations. A portion of the mine's product is railed from site to a range of customers by a single-gauge railway line that extends southward to Thabazimbi where it links into the main railway network. Most coal exports are shipped via Richards Bay Coal Terminal (710km south-east of Grootegeluk) and the rest from the Durban harbour (760km south-east of Grootegeluk). Raw water is delivered to the mine, and to a water-treatment plant on the farm Zeeland by the 700mm-diameter Hans Strijdom pipeline. The pipeline originates at Mokolo Dam, in the Waterberg Mountains, 39km south-east of Grootegeluk. Potable water from the Zeeland water-treatment plant (11km south-south-east of Grootegeluk) is in turn routed to the mine and local communities.
Coal is beneficiated via eight different plants that produce power-station coal (thermal coal) at 35% ash, variously sized metallurgical coal products at different quality specifications and semi-soft coking coal. Thermal coal is sold to Eskom in terms of long-term coal-supply agreements to supply feed coal to the Matimba and Medupi power stations via conveyor belts. Variously sized metallurgical coal products at 15% ash and 11.25% ash, semi-soft coking coal at 10.3% ash, as well as steam coal at 12.5% ash are railed to various customers and shipped to international clients via an export harbour. A small portion of the total product is sold on-site to smaller customers and dispatched by road.
Figure 14: Grootegeluk mine
Table 25: Grootegeluk operation history
Date range | Company | Material notes | |||
1960s – 1980 | Yskor – Iscor – Iscor Mining – Kumba Resources | Drilling exploration holes before mine commissioning took place (221 boreholes drilled) | |||
1980 – 2019 | Kumba Resources – Kumba Coal – Exxaro Resources | Continued exploration drilling post mine commissioning (1 121 boreholes drilled) |
Since beginning exploration activities at Grootegeluk, the company has changed its name and/or unbundled several times without selling the asset to new owners. Through all these changes, exploration drilling continued in the same way.
Small-diameter boreholes (HQ/TNW size core) were drilled on a 500m x 500m grid when the initial exploration project at Grootegeluk started. The suite of analyses performed at that time was analysed only per coal sample and the amount of core obtained from the boreholes was adequate for all the required analysis. Over time, gradual subdivision of coal zones into smaller units or "samples", as well as added relative density fractions to the suite of analysis, resulted in insufficient sample material in some samples and some relative density fractions for the required suite of analyses.
To accommodate the new sample subdivision and in order to have sufficient material available from each sample for the required suite of analyses to relative densities of 2.20g/cc, it was decided to change the size of exploration boreholes from small to large-diameter (123mm-diameter drill core). The large-diameter boreholes were drilled in between the existing 500m x 500m grid of small-diameter boreholes. The reason for this placement of large-diameter boreholes was that analysis of samples from the large-diameter boreholes could be used to supplement analysis of existing small-diameter boreholes where samples and density fractions were absent.
Grootegeluk executes its exploration strategy across the Coal Resource. Boreholes furthest from the open-pit are spaced 3 000m x 3 000m and, closer to the pit, infill holes are drilled to reduce borehole spacing to 1 000m x 1 000m. For the area in front of the open-pit (10 years ahead of planned pit-advance direction), drilled boreholes form a grid of 500m x 500m. In addition, infill holes are also drilled on a 350m x 350m spacing to cover the area that will be mined in the next five years and percussion boreholes are drilled in geologically complex areas to complement the structural interpretation.
Regionally, Grootegeluk is in the southern portion of the Limpopo depression, a relatively small corridor between the Limpopo River in the west and the Palala-Pietersburg plateau in the east. Fundamentally, it is a re-exposed post-Waterberg topographical feature on which Karoo sediments were deposited, followed by tectonic activity, which was the primary element responsible for the development of the depression.
The Zoetfontein fault forms the boundary of the Waterberg coalfield in the north while the Eenzaamheid fault forms the boundary in the south. The Daarby fault, with a throw of some 350m, divides the coalfield into a deep north-eastern portion and a shallow south-western portion. The first fresh coal in the shallow south-western portion is on average 20m below surface. The lowermost coal seam (zone 1) occurs at a depth of about 130m in the shallow portion of the coalfield but this may vary depending on the local structure (Figure 16). The predominantly horizontal coal-bearing formations have a very gentle dip to the south-east near Grootegeluk. Only a few dolerite dykes outcrop in the south-eastern portion of the Waterberg coalfield and no sills have been encountered in any exploration boreholes drilled in the mine right area to date.
The upper part of the coal deposit, the Volksrust formation (±60m thick), comprises intercalated mudstone or carbonaceous shale and bright coal layers. It displays such a well-developed repetition of coal-shale assemblages that it can be subdivided into seven discrete sedimentary cycles or zones (zone 11 – zone 5). Smaller subcycles (samples) were chosen within these zones and sampled individually in the exploration phase. This subdivision of coal seams into smaller lithological units is necessary to cater for numerous mining bench definitions and/or product specifications. The terms "zone" and "sample" are used at Grootegeluk instead of "seam" and "ply" due to the site-specific intercalated nature of the coal and shale. The Volksrust formation is classified as a thick interbedded seam deposit type.
The Volksrust formation zones typically start with bright coal at the base. The ratio of coal to shale decreases from the base of each zone upwards. The basal zone (zone 5) is an exception because of a more homogeneous distribution of coal and shale throughout this zone. The Volksrust formation shale shows an increase in carbon content with depth and varies from a massive bluish-grey mudstone to carbonaceous shale towards the base. Although the thickness and coal quality of the Volksrust formation are reasonably constant across the coal field, a large variation in the yield of semi-soft coking coal and total sulphur content occurs vertically in the coal succession.
The Vryheid formation (±55m thick) forms the lower part of the coal deposit and comprises carbonaceous shale and sandstone with interbedded dull coal seams varying in thickness from 1.5m to 9m. It is therefore classified as a multiple-seam deposit type.
There are five coal zones that consist of predominantly dull coal with some bright coal developed at the base of zones 2, 3 and 4 in the Vryheid formation. Due to lateral facies changes and variations in the depositional environment, these zones are characterised by a large variation in thickness and quality. It is noted in the mine lease area that these zones depreciate in development and coal quality in a westward direction due to sedimentological facies changes. Zone 3 is the best-developed dull coal zone in the mine lease area and reaches a maximum thickness of 8.9m. The basal portion of this zone yields some semi-soft coking coal. Zone 2, on average 4m thick, reaches a maximum thickness of 6m in the mine lease area. The basal portion of this zone also exhibits semi-soft coking coal properties. Zone 2 exhibits the most consistent thickness of all the Vryheid coal zones across the entire Waterberg coalfield. Zone 1, the basal Vryheid coal zone, has an average thickness of 1.38m. Zone 1 contains the best-quality metallurgical coal at Grootegeluk and is suitable to produce char but is not included in the mine plan due to the high stripping ratio given a 12m thick overlying interburden sandstone seam. Due to previous mining activity, over 5Mt of high-quality low-phosphorous content metallurgical coal from zone 1 has been sterilised to date by the pit backfill operation.
All exploration boreholes are logged and sampled by experienced on-site geologists, aligned and in compliance with logging and sampling standards and standard operating procedures. Samples are selected according to seam coal and shale contacts, visual variation in the vitrinite content, assisted by a suite of downhole geophysical logs, and non-coal material present in the seam boundaries. Large-diameter core (123mm) boreholes are drilled for Coal Resource purposes.
Core loss for coal seam intersections is recorded and a recovery of <95% through coal (by volume) is deemed unsatisfactory. Anomalies were investigated and redrilled if required. Wire-line logging results are available for all boreholes. Logging is conducted by recording lithology down to centimetre scale according to the classification of the various coal "lithofacies"/coal type zones or ply (shale-coaly, coal-shaly, coal dull, coal mixed/mainly dull, coal mixed, coal mixed/mainly bright and coal bright) based on the discernible lithofacies change and identified marker horizons, particularly through coal zones.
Sampling of boreholes is only conducted after the stratigraphy has been correlated. The geologist in charge supervises all borehole drilling and is responsible for logging and sampling. Each sample submitted to the laboratory is accompanied by a unique sample number for validation and tracking as well as a submission list that serves as a sample advice sheet with instructions for analysis. The delivery or turnaround time is calculated as the time from which the laboratory receives the samples to the time when the last batch of analysis is reported. Once the laboratory has received and signed the dispatch sheet, the safekeeping and storage of that batch of samples lies with the laboratory.
Grootegeluk uses Bureau Veritas laboratory for its exploration borehole sample analyses. Bureau Veritas acquired Advanced Coal Technology (ACT) in 2013, which had performed Grootegeluk's analysis of exploration borehole samples since the early 1960s. ACT was an outsourced company formed from the old Iscor pilot plant laboratories and has been a continuation of services previously provided by Iscor.
The only form of subsampling conducted at Grootegeluk is the separate sampling of coal and shale layers of the Volksrust formation sample units for analyses. The composited coal and shale samples per sample interval are weighed to determine the samples' relative densities and percentage core recovery. Relative density measurements are carried out at Grootegeluk using the "mass in air versus mass in water" method.
Figure 15: Grootegeluk mine and the adjacent Thabametsi project area
Current sample intervals as per exploration borehole are, in certain cases, subintervals of historic sample intervals. For instance, samples 22A, 22B, 22C, 22D and 22E are subdivisions of sample 22 as it was sampled in historic boreholes hence the nomenclature. When compositing these relevant subintervals, it is fully representative and can be used in conjunction with historic boreholes to describe the same geological unit.
The laboratory follows one of four standard suites of analysis for each sample from Grootegeluk, namely Volksrust formation coal, Volksrust formation shale, Vryheid formation coal and Vryheid formation shale. Coal samples are analysed before shale samples because of potential changes that could take place in the characteristics of the coal due to exposure to the atmosphere.
The analyses performed on the borehole core samples include proximate analysis, ash composition analysis, ash fusion temperature analysis and petrography. Analyses are performed separately on the coal and shale samples after float-and-sink analyses have been performed to obtain fractional samples for the range of densities. All data received from Bureau Veritas is in digital format and checked against the original request list to ensure the required analyses were conducted and results were recorded appropriately. The digital data is then imported into the same database in which the core log data has been captured (Sable Data Warehouse) and subsequent validation procedures are conducted. This serves to verify laboratory accuracy and it is performed during the data-importation stage.
The Coal Resource classification methodology is fundamentally based on SANS 10320 and considers borehole spacing, type of boreholes and structural complexity of the Resource. Additional efforts are used to provide for areas with perceived geological risk.
The classification method is the same for the overlying Volksrust and underlying Vryheid formation Coal Resources for practical considerations. The classification methodology is reviewed each year and reconciliation for that year is used to test the classification criteria. The review addresses specific geological risks expected in the Resource, including increased variability in certain coal qualities, thinning of certain benches by weathering in the Volksrust formation, deterioration of coal formation in certain benches and a gradual increase in the average total sulphur content in general. Only cored boreholes with applicable coal quality data are used and structurally complex areas must be complemented by additional geophysically logged open (percussion drilled) boreholes.
Figure 16: Typical west-east section through Grootegeluk geological model showing the various benches and zones
Table 26: Grootegeluk Coal Resource reporting criteria
Thickness cut-off (thickness and extraction height considerations) | Quality cut-offs (adb) | Geological loss (%) | |||
<0.5m | Ash content of >65% | Variable per bench, calculated each year considering geological model estimation error and physical geological loss |
Table 27: Grootegeluk Coal Resource estimation criteria
Date range | Item | Description | |||
Database | Borehole database | Sable Data Warehouse | |||
Data datum | LO27 WGS 84 | ||||
Number of boreholes used for Resource estimation | 801 | ||||
Validation | Conducted using queries in Sable and Excel | ||||
Data compositing and weighting | Sable Data Warehouse | ||||
Model | Previous model date | 2013 | |||
Last model update | 2016 (conclusion of 2019 update in progress) | ||||
Geological modelling software | Geovia MinexTM | ||||
Estimation technique | Growth algorithm | ||||
Grid mesh size | 20m x 20m | ||||
Scan distance | 2 000m | ||||
Data boundary | 200m | ||||
Model build limits | Upper: limit of weathering Lower: zone 1 floor |
||||
Model outputs | Roof, floor and thickness grids generated for structure. Coal-washability quality grids | ||||
Changes to modelling process | None |
Table 28: Grootegeluk Coal Resource classification criteria
Resource category |
Type of boreholes | Borehole spacing (Volksrust Formation and Vryheid Formation) |
Structurally complex areas | BH/ha | |||||||
Measured | Cored boreholes with applicable coal qualities |
≤500m | Matrix (additional geophysically logged boreholes needed) |
0.04 | |||||||
Indicated | Cored boreholes with applicable coal qualities |
>500m and ≤1 000m | Matrix (additional geophysically logged boreholes needed) |
0.01 | |||||||
Inferred | Cored boreholes with applicable coal qualities |
>1 000m and ≤3 000m | Matrix (additional geophysically logged boreholes needed) |
0.001 |
Table 29: Grootegeluk Resource and Reserve statement
Category | 2019 (Mt) |
2018 (Mt) |
Difference in tonnes (Mt) |
Difference (%) |
Reason for changes | |||||
---|---|---|---|---|---|---|---|---|---|---|
Measured | 2 786 | 2 844 | (58) | (2) | Mining depletion | |||||
Indicated | 1 017 | 1 017 | — | — | ||||||
Inferred | 653 | 653 | — | — | ||||||
Total Coal Resources | 4 455 | 4 514 | (58) | (1) | ||||||
Proved | 2 520 | 2 576 | (56) | (2) | Mining depletion | |||||
Probable | 645 | 645 | — | — | ||||||
Total Coal Reserves | 3 165 | 3 221 | (56) | (2) |
Rounding of figures may cause computational discrepancies.
Table 30: Grootegeluk RPEEE considerations
Item | Criteria | Considered | Comment | |||||
Geological data | Data has been validated and signed off by competent person | Yes | ||||||
Geological model | Geological model was considered and signed off | Yes | Seam depth, seam thickness >0.5m, ash content <65%. Coal qualities reported on an air-dry basis | |||||
Structural model | Structural model was considered and signed off | Yes | 2017 review | |||||
Mining | Mining assumptions considered and defined | Yes | Opencast | |||||
Assurance | Minimum tier 1 assurance (Exxaro governance) | Yes | Resource and LoM done in 2018 | |||||
Economic evaluation |
A concept-level exploitation with economic and mining assumptions, including geotechnical and geohydrological assumptions | Yes | Consolidated exploitation plan | |||||
Environmental | Reasonable demonstration that environmental approvals can be obtained within the context of local, regional and national governmental legislation | Yes | Current required approvals in place | |||||
Tenure | Formal tenure must be demonstrated with reasonable demonstration that a mining right approval can be obtained within the context of local, regional and national governmental legislation | Yes | Mining right (22 years) with reasonable expectation that right will be renewed | |||||
Infrastructure | Assumptions used should be reasonable and within known/assumed tolerances or have examples of precedence | Yes | Current mine infrastructure | |||||
Market | A potential market for the product with a reasonable assumption that this market is sustainable | Yes | Current coal-supply agreements for local and export markets | |||||
No amendments were made to the LoM plan for Grootegeluk in 2019 and the change is only the result of annual mining depletion. All modifying factors were considered, and no downgrade was made to any Coal Reserves in the various categories. The amount of Inferred Resources in the LoM plan is 510Mt, representing 14% of the LoM plan. The impact of Inferred Resources on the LoM plan was tested and is well understood. The Inferred Resources are located at the latter end of the LoM plan and are addressed through continuous exploration.
XPAC mine-scheduling software is used to derive the remaining saleable Reserves from RoM Reserves in the approved pit layout. After converting the geological model's grids to the appropriate format, the floor, roof and thickness data as well as quality data for each bench is imported into the XPAC model. In this model, validations are performed to evaluate the data for possible discrepancies, such as incremental yields anomalies for each bench, thus ensuring they rise with increases in the relative float densities. The Resource category areas are also loaded into the XPAC model for Reserve categorisation purposes.
The XPAC model integrates new geometallurgical principles into the LoM planning process and scheduling model to better predict as-mined plant performance. This is an all-inclusive model that can simulate all the plants in the Grootegeluk complex from one integrated flowsheet. The key improvement is that the model provides:
A number of audits have been conducted, in conjunction with the mine, to ensure the process applied is well-understood, documented and that predicted product volumes are realistic and transparent.
The washability tables for each blast block are imported into the geometallurgical model (XPAC). The geometallurgical schedule imitates reality at Grootegeluk as portions of a single blast block can be allocated to several beneficiation plants in a particular scheduling period. Once the production schedule has run, a blend of blast blocks from different benches is allocated to each plant for each scheduling period. A new composite wash table is then derived for each plant for each scheduling period, which represents the blend of material fed from the mine to that plant. This composite wash table is then used to derive the specific products required to be produced by that plant for that period. A set of calibrated plant factors is applied per plant to adjust theoretical product yields to practical expected levels. It is thus not assumed that a block in its entirety is allocated to one plant only, as this does not represent reality at Grootegeluk. The scheduled mining blocks are of the same size as current actual blast blocks in the mine. The fact that material from different benches is combined and beneficiated simultaneously creates difficulty in reporting saleable product tonnages per bench. The preferred reporting practice at Grootegeluk is therefore RoM tonnes per bench and saleable product tonnes per beneficiation plant.
Indicated Resources are generally converted to Probable Reserves and Measured Resources to Proved Reserves after consideration of all applicable modifying factors. If one or more of the modifying factors have not been fulfilled, Measured Resource is either not converted or the Measured Resource is converted but downgraded to Probable and the associated risk is clearly stated. Inferred Resources are not converted to Coal Reserves.
Table 31: Grootegeluk production figures
Category | Actual 2018 |
FC 2019 |
Actual 2019 |
FC 2020 |
FC 2021 |
|||||
---|---|---|---|---|---|---|---|---|---|---|
RoM (Mt) | 57.2 | 57.0 | 56.2 | 59.8 | 65.3 |
Table 32: Grootegeluk modifying factors considered in converting Coal Resources to Coal Reserves
Modifying factors | Value | |
Geological loss (varies per bench) | 0% – 0.75% for Proved Reserves 0% – 1.5% for Probable Reserves |
|
Thickness cut-off | <0.5m | |
Quality cut-offs | >65% ash content (raw in-situ coal) | |
Mining loss | 0% due to the fact that all mining boundaries are reached, no pillars are left | |
Boundary pillar | N/A | |
Dilution | Applied to in-situ mineable Reserves due to the inter-layered composition of the deposit | |
Contamination (varies per bench) | 0.0 – 0.75 metres applied to interburden seams | |
Mining recovery efficiency (varies per bench) | 0.0 – 0.75 metres depending on bench height | |
Planned average slope angles | <61.7 degrees | |
Practical plant yield | Considered in the reserving process as per wash table information per combination of blocks per planning increment and the empirically determined practical yield adjustment factor | |
Strip ratio cut-off | Energy strip ratio >7GJ/ex-pit tonne | |
Environmentally sensitive areas | Areas underlying wetlands and other eco-sensitive areas are excluded from the Reserves with a 100m or 100-year floodline cut-off applied | |
Legal | The layout is within the mining right boundary and not closer than 15m | |
Social | There are no known socially sensitive areas in the pit layout (for example, graveyards and dwellings) | |
Geohydrological | Areas identified are flagged and excluded or reclassified in the reserving process |
We do not know of any pertinent risks or other material conditions that may impact on the company's ability to mine or explore, including technical, environmental, social, economic, political and other key risks.
There are a number of low risks addressed by continuous actions at the operation:
Geological structure accuracy: The structure interpretation (fault positions) is based on current points of observation. Additional percussion boreholes are required in structurally complex areas to finalise the position and characteristics of faults.
Inferred Resources: Some 15% of the total Coal Resource (~14% in LoM plan) is in the Inferred category due to the revised mining pit introduced in 2017. The impact of the Inferred Resources are known, occur on the tail-end of the LoM plan and are addressed by an integrated exploration plan that is reviewed every year.
Thinning of upper benches: Bench 2 and bench 3 are thinning, and are not present in certain areas of the Coal Resource due to weathering with only a small portion of bench 2 remaining in the next few years. This information has been incorporated in the mine's production schedules. Large portions of bench 2 and bench 3 are still available in the planned pit layout further away from the current production face.
Increasing total sulphur content in semi-soft coking coal: A trend of increasing sulphur content in the benches used to produce semi-soft coking coal (benches 2, 3 and 4) is observed in the geological model. Coal sulphur content is known to be highly variable, which makes it difficult to estimate accurately. The variability was considered during the revision of the 2017 pit and LoM plan.
Phosphorus content in semi-coke feed coal: The phosphorous content of bench 11 poses a risk to the production of semi-coke. Bench 11 and zone 1 are the sources of relatively low phosphorus content coal but bench 11 shows a continual increase in phosphorus content. Studies conducted show that most of the phosphorous content of bench 11 is in the uppermost portion of the bench and can be removed separately to mitigate the risk. In addition, zone 1 (bench 13) is currently omitted from the mine plan due to its high-stripping ratio but can be used as a sweetener if it is blended with bench 11.
Reserve within the Thabametsi mining right: A small amount of the Inferred Coal Resource inside the Grootegeluk LoM is located within the adjacent Thabametsi mining right. Both mining rights are held by Exxaro. The risk is not deemed to be material.
The implementation of a short-term geological model that incorporates exploration, infill and production drilling as well as pit mapping will enhance short-term estimation and mine planning significantly. The implementation of the GG6 beneficiation plant is unlocking exceptional value in the semi-soft coking coal market.
An update of the geological model is near completion. A subsequent review process of the exploitation strategy of the Grootegeluk complex is currently under way. The review includes evaluating various alternative products, pit layouts, overburden strategies as well as optimal coal bench definitions. The review will be concluded during 2020.